Better battery production through surface science
How interfacial testing can improve lithium-ion battery design
Set the standard in an industry where there is none
Advances in lithium-ion battery (LiB) technology are accelerating. Fueled by growth in the EV market, demand is skyrocketing. Suppliers must scale up while ensuring consistent product performance and process efficiency. Whether it’s cutting-edge research or commercial production, testing provides the information that drives innovation.
More than accuracy and precision, reliable testing requires consistency – not just test-to-test, but across the entire development and production cycle. However, in an industry still evolving, standardized testing, using the same high-quality technology, diagnostic software, and processes, is an anomaly. But it does exist.
We help bring your innovation to the surface
When it comes to developing and producing the batteries that will enable the future, the next leap in innovation lies just beneath the surface. Revealing it requires a careful process of developing, testing, refining, and retesting. Potential innovation lies at the intersection of surfaces.
Interfacial testing is vital for grasping how different liquids and solids interact. It's crucial at various stages of making lithium-ion batteries, such as slurry formulation, coating, wetting, calendaring, drying, and formation.
Read our application guideHow to improve coatings and adhesive bonds in battery production
The durability of lithium-ion batteries is closely linked to the coating adhesion strength of lithium-ion battery electrodes. Testing the adhesion strength allows prediction of the mechanical bond before it is used, saving time and money.
Watch our webinar on demand by our application expert Dr. Daniel Frese and learn about how the adhesion strength between the electrode coating and the base material affects your battery's quality. Discover how to measure and enhance this important property.
Watch webinarWhy researchers should embrace interfacial testing and analysis
Electric vehicles rely on lithium-ion batteries (LiB) to improve the driving range of electric vehicles and make them comparable to their gasoline-powered counterparts. Just like many other industries, LiB companies need to adopt standardized production methods to make high-quality products and meet the growing demand.
Find out why a standardized testing program, including thorough testing and analysis of interfaces, is crucial for the success of LiB researchers and manufacturers as production increases.
Download whitepaperOur instruments bring your battery production to the next level
When it comes to testing instrumentation, KRÜSS offers unmatched product breadth and depth of engineering. Our LiB portfolio features drop shape analyzers and tensiometers that are regularly regarded as among the most precise, accurate, and easiest to use. Designed and engineered at our global headquarters in Germany, they cover a range of applications.
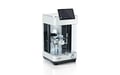
Tensíío
The new generation tensiometer for liquid and solid surfaces
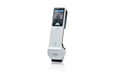
Ayríís
Surface quality control has never been so easy and reliable
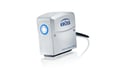
MSA One-Click SFE
Analyzing wettability in a second with only one click